GRAFTA Nanotech
GRAFTA™: Graphene based nanotechnology for the remediation of mining and industrial waste water.
White Paper
Table of Contents
In 2011, Dr. Edwin Safari Ph.D., P.Eng. (Safari) started research exploring different aspects of graphene and graphene oxide due to its range of exceptional properties.
​
It was not long after the Nobel Prize winning discovery of graphene nanosheets in 2004, that various research disciplines including environmental remediation started an exponentially growing exploration of its various “miraculous” properties. Safari’s research was no exception, exploring the adsorptive capacity of graphene and graphene oxide, the ability to functionalize and tackle various contaminant removal challenges, and particularly ways to minimize the cost through mass production and feasible use in a competitive environmental remediation market.
​
The massive specific surface area of graphene at its nanoscale of about 2600 m2/gram, potentially and practically provides an excellent platform for the adsorption of contaminant molecules. The unique bonding of contaminants and the possibility of engineering graphene through adding virtually any other molecules to enhance adsorption and absorption are amongst the main characteristics of graphene, making it a high-potential candidate for the next generation of environmental remediation products.
​
With the help of graduate students, Dr. Safari’s work examined the ability of graphene and graphene oxide to remove different types of contaminants, their fate and transport in porous media, and their interaction with biological growth within porous media using strong landfill leachate.
​
Safari’s research proved that nano-scale graphene is indeed unique in adsorption and nano-engineering capabilities to tackle a variety of environmental remediation issues.
​
However, using graphene and graphene oxide in environmental remediation applications has been facing major challenges in terms of mass production and usage practicality. Producing graphene and graphene oxide through chemical methods such as micromechanical and liquid phase exfoliation of graphite, Hummer’s method for producing graphene oxide and chemical vapor deposition have proven to be commercially unviable due to extensive use of chemicals (strong acids), complicated process and of consequently, the associated costs.
​
Research leading to GRAFTA™ aimed at a production method using which graphene and graphene oxide could be produced at large industrial scale and be practically deployable as an efficient treatment medium for contaminated aqueous solutions.
Introduction
Graphene Overview
Graphene-based materials are gaining heightened attention as novel materials for environmental applications. The unique physicochemical properties of graphene, notably its exceptionally high surface area, electron mobility, thermal conductivity, and mechanical strength, can lead to novel or improved technologies to address the pressing global environmental challenges.
​
Graphene is a two-dimensional layer of carbon atoms arranged in a hexagonal crystalline structure. Graphene, in its pristine form, is composed of a single layer of carbon atoms arranged in a sp2-bonded aromatic structure as shown in Figure below.
​
Graphene contains no oxygen in its structure while graphene oxide contains a small amount of oxygen with a typical carbon to oxygen ratio of 2 to 4.
​
Reduced graphene oxide (rGO) contains much less oxygen compared to graphene oxide with a carbon to oxygen ratio of 8 to 246. In some other studies (Ersan et al. 2017) it was also indicated that GO can contain between 10.4% and 54.4% oxygen and rGO can also contain between 17.5% and 31.3% oxygen.
Graphene, in its pristine form, is composed of a single layer of carbon atoms.
Graphite can be exfoliated to generate single or multi layer graphene.
This was initially demonstrated by micromechanical exfoliation, the sequential cleavage of graphite to graphene using adhesive tape.
This simple approach to produce pristine single-layer graphene sheets was used by Geim abd Novoselov in their pivotal work on the electronic properties of graphene, leading to the Nobel Prize in Physics in 2010.
The above represents the theoretical values. Materials generated at nano scale can contain different types of graphene-based structures.
Differences between GO and rGO are in their functional groups on the surface, crystal structure, optical property and defective structure.
Graphene Oxide shows strong acidity, with high adsorption for cations and basic compounds.
​
Graphene, however, has a hydrophobic surface and due to strong π-π interaction, it has high adsorption capacity to chemicals and organic compounds.

Contaminant Removal with Graphene
Graphene and graphene oxide in original and functionalized forms have shown high capacities in adsorption of heavy metals such as lead, mercury, chromium and cadmium and organic compounds such as metformin (an emerging organic contaminant), naphthalene and methylene blue.
It has so far been established that different nano scale graphene-based materials are highly capable of removing different types of contaminants including emerging contaminants that might be difficult to remove. However, no industrial scale application has been reported using any type of graphene. There are three primary reasons behind lack of industrial application of graphene based nano scale materials in environmental remediation as follows:
-
Evidence of toxicity of graphene-based materials at nanoscale when released into the environment;
-
Practical limitations in recovery of used adsorbent from aqueous solutions in real world (e.g., groundwater);
-
High cost of production; cost of production of GO and rGO at nanoscale can be as high as $700 per 1 gram of material and more.
It should also be noted that the majority of research if not all, has been conducted on single contaminant aqueous solutions with only a few cases on multi-contaminant, typically synthetically spiked solutions. Despite several recently published reviews on water purification technology using graphene and its derivatives, there is still a considerable gap regarding multiple water-pollutant remediation using advanced graphene materials. The extensive research has been using almost only nano-scale graphene-based materials and rarely any practically (and none commercially) viable graphene-based material has been studied.
The Vision of GRAFTA™
Graphene nano-sheets, although offering much potential, have been prevented from emerging in the environmental remediation market due to an extremely high cost of production and unknown risks to human and ecological health associated with exposure to nanomaterials.
This opportunity triggered Safari to focus research on possible methods of producing a graphene-based material in a low-cost manner and to prevent release of nano-scale graphene to the environment to prevent potential (not extensively known yet) risks.
Upon approval of his proposal, he continued the research at Carleton University (Ottawa, Ontario) in 2016, through a competitive Natural Sciences and Engineering Research Council (NSERC) grant. He formulated and optimized the structure of what is now trademarked as GRAFTA™ (at laboratory scale and proved its outstanding performance in removal of contaminants.
GRAFTA™ stands for a Graphene Based Solution for Terra and Aqua (earth and water).
GRAFTA™ Structure
To address the challenges that have restricted graphene in the commercial market of water and wastewater treatment and remediation, Safari determined that the graphene-based material should have the following properties:
-
A structure that can be easily applied to large-scale treatment/remediation projects;
-
Take advantage of immense adsorption capacity of graphene and graphene oxide nano-sheets;
-
Be produced without the use of environmentally harsh chemicals;
-
Be produced and supplied at a low cost and affordable market price;
-
Have the capability of being regenerated or safely disposed of after saturation.
The solution to the above challenges was found to be in using waste materials in combination with organic materials capable of producing multi-layered graphene and graphene oxide through a facile thermal reaction.

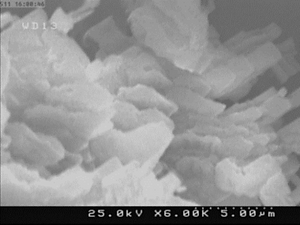
Examples of GRAFTA™ Structure
Using inert waste material and organic substances capable of graphitization, GRAFTA™ was generated at a substantially lower cost compared to nano-graphene and graphene oxide.
GRAFTA™ is essentially a micro-scale particle with nano-scale graphene and graphene oxide layers formed over the surface. As a result, the thermally induced strong chemical bond eliminates the possibility of nano-scale graphene and graphene oxide release into the environment, making it suitable for in-situ applications.
The main advantages of GRAFTA™ are as follows:
-
Low cost;
-
Extremely high adsorption capacity for heavy metals such as mercury, lead, cadmium, chromium, selenium etc;
-
Extremely high adsorption capacity for PHCs, VOCs, Chlorinated Compounds etc.;
-
Near Zero Leaching of Contaminants after use;
-
End of Life GRAFTA™ can potentially be used in construction;
-
In-Situ Injection for Groundwater Remediation and Permeable Reactive Barrier;
-
Possible use in Low Impact Development (LID) for In-situ Treatment of Infiltrating Water.
GRAFTA™ Characterization
GRAFTA™ was characterized using techniques applicable to materials and particularly nanomaterials characterization, including Scanning Electron Microscope (SEM), Transmission Electron Microscope (TEM) as well as Raman Spectroscopy and X-Ray diffraction.
Formation of nano sized layers of carbon layers was evident in both SEM and TEM images. Chemical composition analysis was also performed to identify the key elements formed.
According to our hypothesis, the ideal composition would be a high percentage of carbon, some oxygen (mainly resulting from the breakdown of organic matter). The average ratio of carbon to oxygen was 4.19 to 5.37 (on a molecular weight percentage basis) which is more consistent with typical reduced graphene oxide (rGO).

An example of SEM image along with elemental analysis
An example of SEM image of GRAFTA™ indicates the presence of carbon along with smaller percentage of oxygen in agreement with the theoretical values presented in the literature.
The TEM images indicated layered structure of graphene and graphene oxide which could range from multiple to several layers and clustered over the base substrate in numerous numbers. In the TEM images, the lighter areas indicate a smaller number of graphene layers. Each nano-sheet provides a considerably large surface area for adsorption through mostly Van Der Waals forces along with a more rigid bonding of cationic compounds with graphene oxide.
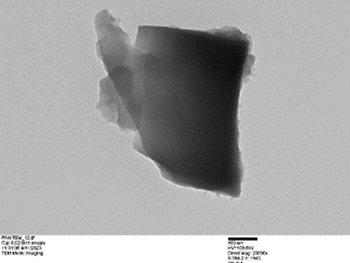
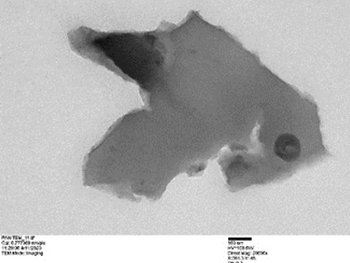
Examples of GRAFTA™ Structure under TEM
To confirm formation of graphene on the surface of the base glass, some of the samples were analyzed using XRD. The following figure show XRD patterns for Samples 15, 20 and 24 respectively. XRD patterns of rGO are represented by a broad peak at about 2ÆŸ of 23.5º. This has been the case for the three samples analyzed for XRD pattern.
Raman spectroscopy is a common method for identifying the structure of graphene-based materials. Graphene typically shows a peak in Raman shift at about 1570 to 1580 cm-1. The higher the intensity, the higher the number of layers of graphene forming graphite.

Example XRD pattern for GRAFTA™

Example Raman Shift for GRAFTA™
Raman shift peaks at about 1570cm-1 for GRAFTA™ which clearly indicates multilayer graphene formation over the substrate base.
As shown in the example Raman Spectroscopy Figure, the D band Raman shift peaks at around 1370cm-1 and the G band peaks at 1580cm-1. This is in confirmation with the structure of graphene or crystalline graphitic structure. However, given the high intensity of the peaks, a high number of graphene layers can be concluded.
GRAFTA™ Line of Products
Currently, two GRAFTA™ products are being produced.
GRAFTA™1.0 (G1) is the original non-altered GRAFTA™ product that consists of graphene and graphene oxide nanosheets.
Understanding the market demand on resolving their water treatment issue where nitrate and selenium in form of selenate were the main challenges with no feasible solution in the horizon, G1 was modified to introduce a product that is amended with a reducing agent working closely with the graphenic structure of GRAFTA™ to chemically reduce target contaminants followed by adsorption of the lower oxidation state reaction products or reduction byproducts. This product is currently labeled as GRAFTA™2.0 (G2).
Nitrate, found in many mining sites at relatively high concentrations, is reduced to ammonia using G2, which in turn is adsorbed by the graphene structure in both G2 and G1.
Selenium removal was found to be challenging using the current removal methods which are mostly relying on biological processes. G2 simply reduces the selenate into selenite and elemental selenium which is adsorbed by the graphenic structure of both G2 and G1 leading to an effluent that persistently contains mostly non-detectable concentrations of selenium.
GRAFTA™ Application Forms
In general, GRAFTA™ line of products can be used either in above-ground (onsite) form (e.g. tanks and vessels) or in in-situ form through injection into groundwater systems to form permeable reactive barriers (PRBs).
In most cases, an up-flow hydraulic regime is preferred for a slight expansion of the GRAFTA™ packing for higher contact surface area.

A typical cross section of a vessel housing GRAFTA™
Performance of GRAFTA™
GRAFTA™ in its original form, with no alteration and engineering is a combination of graphene and graphene oxide nanosheets that have shown to be highly capable of adsorbing heavy metals and organic compounds from aqueous solutions.
Bench scale tests mostly conducted in the form of adsorption column tests along with batch adsorption tests (also known as isotherm tests) have been conducted for a variety of contaminants including heavy metals, organic compounds, and inorganics such as nitrate, phosphate, and sulfate, mostly for real-life contaminated waters from mining related tailing waters, oil and gas produced water, landfill leachate, and few other industrial wastewaters along with some water samples spiked with certain target contaminants.
The key advantage of using GRAFTA™ is that it simultaneously adsorbs both heavy metals and tough to remove organic compounds such as chlorinated solvents, petroleum hydrocarbon, polycyclic aromatic hydrocarbons (PAHs), Volatile Organic Compounds (VOCs) such BTEX (benzene, toluene, xylene, ethylbenzene) and more importantly PFAS which is currently under further investigation.
Recent performance test for the removal of a variety of metals including but not limited to copper and selenium from mining tailing waters, indicated that GRAFTA™ can remove these metals to nondetectable concentrations.
Typical retention times required to adsorb contaminants by over 90% removal efficiency is about 15 minutes to 45 minutes.
Heavy Metals Removal Using GRAFTA™
Extensive testing of both G1 and G2 using real-life and spiked waters, indicated that majority of heavy metals including but not limited to mercury, selenium, lead, arsenic, manganese, chromium, cobalt, cadmium and uranium are removed by G1 and G2 where applicable.
In some mine waters, selenium, being the main contaminant of concern, is present in form of selenate which along with relatively high concentration of nitrate makes the treatment challenging. To tackle the challenges, G2 which is amended with a reducing agent was used to effectively reduce selenate to selenite and elementals selenium which was then adsorbed by the graphenic structure of GRAFTA™.
A summary of the removal efficiencies using G1 and G2 for a variety of waters contaminated with heavy metals is presented as follows:

Organic Contaminants Removal Using GRAFTA™
G1 is most suited for a direct adsorption of organic contaminants including but not limited to petroleum hydrocarbons (F1 to F4), BTEX (benzene, xylene, ethylbenzene and toluene), chlorinated compounds (tetrachloroethylene, trichloroethylene, vinyl chloride and chloroform), phenolics (pentachlorophenol etc.), Polycyclic aromatic hydrocarbons (PAHs) at very high rates.
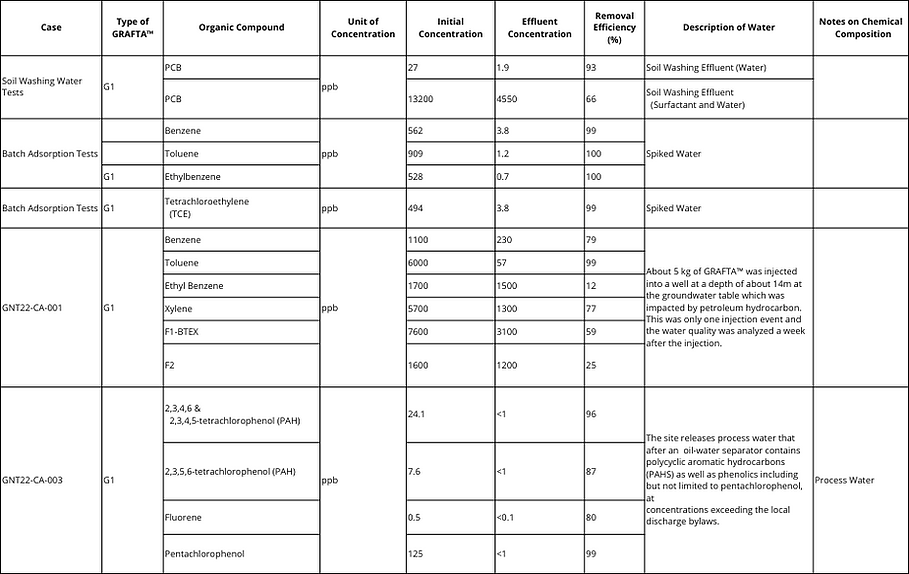
Inorganic Constituent Removal Using GRAFTA™
GRAFTA™ being a carbon-based adsorbent, was not necessarily designed for removal of inorganics such as nitrate, phosphate, sulfate and carbonate. However, experiments conducted on various waters with relatively high concentration of total dissolved solids (TDS) indicated that phosphate and ammonia are directly adsorbed by GRAFTA™ (G1).
However, considering the rising demand of the industry, in particular the mining sector, to remove relatively high concentrations of nitrate in tailing waters, GRAFTA™ was modified with a reducing agent to chemically reduce nitrate to ammonium, followed by adsorption of ammonium within the same reactor (vessel) on the graphenic structure (G2).

End of Life GRAFTA™ Management
GRAFTA™ as an adsorbent is subject to saturation and reaching its adsorptive capacity for various contaminants. The adsorptive capacity of GRAFTA™ (G1 and G2) can be exhausted upon permeation of hundreds to over a few thousand pore volumes as evidenced based on bench scale column tests conducted so far.
Used GRAFTA™ (not necessarily at the end of life) has been tested for leaching contaminants in accordance with Toxicity Characteristics Leaching Procedure (TCLP) and the results have indicated that leaching is minimal and, in all cases, (for metals) below the regulatory limits set in Canada (more specifically Ontario).
Upon saturation however, management of the end-of-life product becomes critical. In general, there are three avenues for end-of-life GRAFTA™ management:
Landfilling: Upon verifying the leaching compliance with applicable land disposal regulations (in Canada and elsewhere), the simplest option for end-of-life GRAFTA™ would be disposal in a regular landfill or hazardous landfill based on the standard TCLP results.
Reuse: Considering the fact that GRAFTA™ has physical and mechanical properties similar to fine sand and the fact the leaching of contaminants is minimal, it can be used in a variety of construction schemes, such as applications in road base or subbase material or low strength concrete, or as landfill intermediate or final cover which might be beneficial as it can act furthermore as part of a biocover system. These uses, however, should be verified on a case by case basis and a general rule may not be applied.
Regeneration: regenerating used GRAFTA™ for metals and organic compounds can theoretically be accomplished through desorption of contaminants using strong acids and organic solvents respectively. However, given the cost and complexity of the process, this option may not be economically feasible. Regeneration of GRAFTA™ used for adsorption of organic compounds (except for PFAS group of compounds) can also be achieved through thermal processes such as thermal desorption and incineration). However, these options should be explored and evaluated on a case by case basis.
Conclusion
GRAFTA™ has proven to successfully remove a wide range of contaminants including but not limited to heavy metals (mercury, arsenic, lead, uranium, selenium, copper and nickel to name a few), organic compounds such as petroleum hydrocarbons, chlorinated solvents, PAHs and PCBs.
The adsorptive capacity of GRAFTA™ is owed to its graphemic structure, where thousands of multilayered graphene and graphene oxide nanosheets are available, firmly grown on an inert base substrate. This provides a very large surface area for adsorption and through a variety of adsorption mechanisms including Van der Waals and covalent adsorption. Organic contaminants are mainly adsorbed onto the graphene layers while heavy metals are adsorbed on the graphene oxide, both present on GRAFTA™ micro-sized particles. A suitable ratio of carbon to oxygen is maintained through the production process to achieve this unique combination.
GRAFTA™ in its original form is considered an adsorbent, while an amended version of GRAFTA™ (i.e. GRAFTA™2.0) is engineered with a reducing agent, which has broadened the range of target contaminants to include nitrates, phosphates and sulfates. GRAFTA™2,0 has shown outstanding performance in removing selenium mostly found in form of selenate through chemical reduction of selenium to selenite and elemental selenium followed by adsorption on graphene oxide.
Experiences with a variety of tailing waters in Canada, have proven the capability of GRAFTA™ and in particular GRAFTA™2.0 in removing high concentrations of nitrate and selenate, in a reliable manner, lowering the concentrations well below typical applicable regulatory limits.
GRAFTA™ has proven to have significant longevity in removing key contaminants of concern such as selenium and in some cases, breakthrough is not achieved even over 5000 pore volumes of permeation.
Leaching of adsorbed metals, has shown to be minimal and in most cases well below the regulatory limits set for hazardous waste, making the disposal of end-of-life GRAFTA™ products affordable.